Date: 19 May 2022
Time: 13.45 - 16.35
Keynote
13.45 - 14.25
Professor Johan Trygg, UMEÅ, Sweden
Presentations
14.25 - 14.50
Manager Dairy Aseptic Solutions Bengt Eliasson, Tetra Pak, Sweden
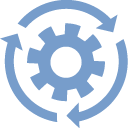
14.50 - 15.15
Programme Manager, Karen Sørensen, DRIP Partnership, Danish Agriculture & Food Council, Denmark
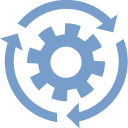
15.45 - 16.10
Principal Scientist Klavs Martin Sørensen, FOSS Analytics, Denmark
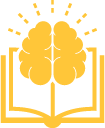
Flash talks
16.10 - 16.22
Product Technician John Lea, Norrmejerier, Sweden
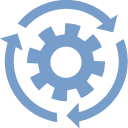
16.23 - 16.35
Professor Martin Grunow, TUM School of Management, Technical University of Munich, Germany
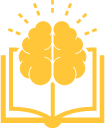
Abstracts
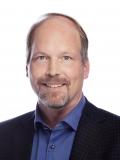
Dairy optimization - key drivers for future dairy efficiency
In dairy production, there is a clear need to better understand the process itself, and interaction with starting materials in order to make the process more automated and optimised. Supply chain variability transfers into variability of the final product quality with difficulties to predict product quality and shelf life. This has negative impact on dairy effectiveness, competitiveness and sustainability of the system and contributes to increased insecurity in food supply. To overcome these limitations, in-depth characterisation of the whole production process is important. This needs to be done with application of Quality by Design (QbD) approaches that will keep the causal link between each process step and relations between all important process variables. Increased systems understanding can primarily be achieved by experimentation, which nowadays can be done in a fast and fully controlled way by application of automated high-throughput small-scale bioreactor systems, such as the ambr250 system, designed for parallel operation and automated sample analysis of critical process parameters. In such systems, large amounts of data are generated and then comes the challenge of utilising them to create information and process knowledge. Here, adoption of multivariate analysis (MVA) methods provide an opportunity for real-time monitoring and further optimization of dairy processes.In the presentation I will describe how process development and optimisation can benefit from such high throughput systems in combination with AI/machine learning tools, resulting in the creation of digital tools for process optimisation, monitoring and control and how the opportunities that digitalisation brings may result in new ways for the food industry, increasing its productivity and competitiveness and being an important part for a sustainable growth and employment.
Professor Johan Trygg, UMEÅ, Sweden
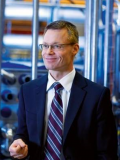
Equipment & line configuration for optimal performance
The dairy industry is under pressure in many ways. The consumption of liquid dairy products is stagnant in the Nordic countries although we see a small growth globally. The competitive situation is intense which sets new demands to continuously reduce the production cost. Also, there is a strong and increasing demand from society to improve the environmental footprint on products in the marketplace.The good news is that over the recent years, several new ways to improve the performance of liquid milk production lines have been introduced. These range from recovery solutions on plant level to optimised setup of specific production lines to new or improved features on dairy unit operations. This can be combined with the latest technology findings to make the production solutions even more efficient. Several examples on how energy consumption, food waste, water usage and cleaning demands can be significantly reduced will be given, without compromising production flexibility or final product quality.
Manager Dairy Aseptic Solutions Bengt Eliasson, Tetra Pak, Sweden
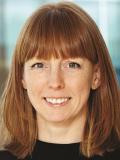
Safe water reuse in the food industry - a triple helix approach
DRIP - A triple-helix interdisciplinary innovation partnership between major water end-users from the food and beverage industry, water technology providers, knowledge partners and authorities has shown ways to create effective solutions to improvement of water efficiency in the food industry without compromising on food safety. The partnership aims at a paradigm shift in industrial water efficiency through demonstration and implementation of a water-fit-for-purpose concept to use significantly less water of drinking water quality and increasingly use recycled and reclaimed water. Ensuring the quality of water throughout its use is of paramount importance to secure food safety and product quality. Having Danish food and environment authorities as associated partners in the project allowed for a positive co-operation and dialogue with a focus at very early stages on important considerations regarding regulation.While water savings and reuse are the starting point for initiation of pilot and full-scale projects in the partnership, other factors like e.g. associated energy and resource savings and released wastewater treatment plant capacity are also key to provide business cases with attractive payback times. Comprehensive mappings of resource flows in terms of water, energy, materials, products and waste through the factories (brewery, poultry abattoir, pig and cattle slaughterhouses, meat processing plants, fishmeal, dairy) provided the foundation for developing attractive scenarios for increased water efficiency. 20 of the most promising scenarios have been further matured into pilot and full-scale implementation projects. Estimates for the DRIP pilot and full-scale projects show that the entire project portfolio has a total water savings potential of 25 % when fully implemented in full-scale operations.The partnership consists of 18 partners from the food industry, technology providers and knowledge partners. The Danish Veterinary and Food Administration and the Danish EPA are associated partners. The partnership is funded by Innovation Fund DK.
Programme Manager, Karen Sørensen, DRIP Partnership, Danish Agriculture & Food Council, Denmark
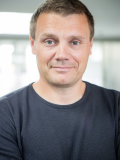
Measuring where and when it matters
Advanced chemical sensors are beginning to become abundant in the industry. The last decades of advances in sensor development have produced relatively cheap and very robust chemical sensors that can ensure that a given production always runs at an optimum with no scraps or rejects through on-line measurements and process analytical technology. Sensors can be put at key locations through the production process and generate large amounts of very complex data, giving near-instantaneous fingerprints of the chemical composition of a process stream. All these sensors will generate massive amounts of data that needs to be stored and handled correctly in order to reveal its full value. Producing a lot of data quickly is in and by itself not very useful – the data must be relevant and of a very high quality as well. In this talk I will demonstrate how the careful processing of data generated from complex sensors can be combined with multivariate data analysis and machine learning to generate relevant knowledge under the premise: to make measurements only where and when it matters.
Principal Scientist Klavs Martin Sørensen, FOSS Analytics, Denmark
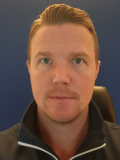
Waste and optimization in production
With dairies getting larger, with more and more production, it is of utmost value to minimise waste throughout production. We have only one planet to take care of, and all the waste produced has a major effect on the environment. The Nordic countries should be in a position to lead with this issue. Waste is unused resources from all types of production and can be categorised into unused raw material i.e. milk, refined product, water, packaging material, energy and personnel. All of these should be reviewed when considering waste and are all equally important. Through minimising the product waste of raw milk, finished product and chemicals are probably where most dairies could lessen the environmental impact and at the same time save a lot of money. This can be done by better planning throughout the facilities and systems to retain the waste product, for example, by installing modern conductivity or turbidity sensors and filtration systems product can be rescued from going down the drain. In reality, this could be as much as 6% depending on the kind of product line and facility. A biogas plant can be a supplement for the excess waste that the dairy cannot retain in any other way.
Product Technician John Lea, Norrmejerier, Sweden
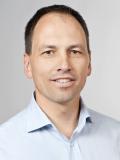
Are dairy concentrates more sustainable than powders?
Food manufacturers introduce more environmentally friendly processes to account for increasing sustainability concerns. However, these processes often accompany a reduction of product shelf life, limiting the delay of sales to future periods with higher prices. A framework has been developed to analyse the impact of shelf life on the trade-off between economic and environmental performance of two types of dairy products. Since the differences in shelf life have their key impact at the tactical planning level, an optimization model has been developed for this aggregation level. Its objectives reflect profit and relevant environmental indicators. A rolling horizon scheme is used to deal with price uncertainty, using Eurex futures as price predictors. The framework uses these tactical planning results for strategic decisions on product and process selection.A case study contrasts traditional milk powders against novel milk concentrates. Concentrates require less energy in processing but have a shorter shelf life. Results show that powders offer a potential profit benefit of up to 34.5%. However, this economic value of shelf life is subject to a priori perfect price knowledge. If futures are used as price predictors, the value of shelf life is reduced to only 1.1%. The economic value of shelf life is therefore not a strong argument against the substitution of powders with more environmentally friendly concentrates. Two objectives, profit and eutrophication potential, are shown to be sufficient to capture trade-offs in the case. Several product mixes are determined that omit powders and perform well with regard to profit and environment.
Professor Martin Grunow, TUM School of Management, Technical University of Munich, Germany