Date: 20 May 2022
Time: 12.25 - 16.15 (lunch included)
Keynote
13.25 - 14.05
Professor Ulrich Kulozik, Technical University of Munich, TUM School of Life Sciences Weihenstephan, Germany
Presentations
14.05 - 14.30
Corporate Scientist Ralf Krack, Ecolab, Germany
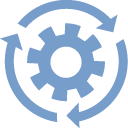
14.30 - 14.55
Professor Frank Lipnizki, Department of Chemical Engineering Lund University, Sweden
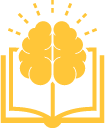
15.15 - 15.40
R&D Membrane Engineer Oliver Geschke, Alfa Laval, Denmark
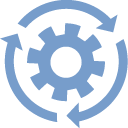
15.40 - 16.05
Professor Murielle Rabiller-Baudry, Institut des Sciences Chimiques de Rennes (ISCR) University Rennes, France
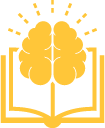
Abstracts
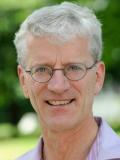
Membrane filtration in the dairy industry - opportunities and challenges
Membrane technology has been widely established in dairy operations for concentration and fractionation of milk and whey by means of micro-, and ultrafiltration, reverse osmosis or combinations thereof. It is not exaggerated to say that membrane technology has been one of the key drivers for innovation in the dairy industry over the last decades reaching back to its first application in the 1960s in New Zealand.This presentation focuses on aspects of membrane fouling of membrane surfaces and presents recent results that help to better understand and to mitigate this unwanted phenomenon in view of options to improve flux and targeted transmission of components. A key factor is the effect of length on deposit formation resulting from the loss of static pressure along the flow path in crossflow membrane filtration, which has been recognised a long time ago and which resulted in the concept of uniform transmembrane pressure operation (UTP). This principle can be extended and applied also in other module types than ceramic tubular membranes, even in spiral-wound membranes (SWM). Another important aspect is a deeper understanding of molecular interactions of components with the membrane surface and within the deposited material, which assists in understanding variability of flux and transmission, e.g. in milk protein fractionation by microfiltration and protein concentration by ultrafiltration. Based on novel insights, possibilities for new membrane technological concepts for dairy applications will be proposed and discussed with regard to practical pros and cons. Also, module concepts such as tubular, spiral-wound and hollow-fibre systems will be compared with regard to energy consumption and filtration efficiency.
Professor Ulrich Kulozik, Technical University of Munich, TUM School of Life Sciences Weihenstephan, Germany

Membrane cleaning for dairy industry - optimising water and energy consumption
All industries strive for continuous improvement. Industries using membrane-based processes are a good example. Since membranes started being used in the Dairy Industry, some 40-50 years ago, there has been a continuous stream of improvement steps. In the early days, it started with flat sheet membrane systems. The cleaning of those membranes was not very well understood and not very efficient at the time. The early flat sheet membrane systems used roughly 20 litres of cleaning solution per square metre membrane surface, per cleaning step. Typically, four to five steps were needed to get those systems cleaned. The systems themselves were small in membrane surface compared to today’s spiral wound membrane systems. The cleaning of the membranes has also undergone significant change during those years. For the first spiral wound systems, 5-6 litres of cleaning solution were used per square metre, per cleaning step. However, today no more than 1-3 litres per square metre membrane surface is utilised. The original flat sheet systems were often cleaned at 60 to 70°C depending on the type of membrane. The later design and the construction of the spiral wound membranes restricted temperatures to about 50°C. More recently, temperatures have been permitted to rise further since the introduction of the pHt membranes, allowing cleaning temperatures up to 70°C and hot water sanitation steps even up to 90°C. This presentation will cover the limits of optimisation in terms of water and energy consumption and the best way to find the most economic methods of cleaning and sanitizing membrane systems in dairy applications.
Corporate Scientist Ralf Krack, Ecolab, Germany
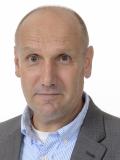
The future of membranes in the dairy industry: Processes, modules and applications.
The dairy industry was one of the first industries, outside the water industry, adopting membranes in the 1960’s. Since then, membranes have become established in the fractionation, concentration and clarification of various dairy products ranging from milk to whey and cheese. This presentation provides an outlook into the future of membrane processes, modules and applications in the dairy industry.The first part of the presentation will focus on new applications of the conventional membrane processes; microfiltration, ultrafiltration, nanofiltration and reverse osmosis. This will be followed by a discussion of applications of the emerging membrane processes; forward osmosis, membrane distillation, electrodialysis and pervaporation. The potential and limitations of these emerging processes in the dairy industry will be covered, e.g. the use of forward osmosis for whey concentration and electrodialysis for whey demineralisation. Following on, new membrane modules will be discussed such as vibrating modules and rotating ceramics discs which minimise the effect of concentration polarisation and reduce membrane fouling. Furthermore, opportunities to improve performance of current modules by processes e.g. back-pulsing will be included. The final section will review the opportunities of membrane processes in the water loop of the dairy industry by either recovering water in production using nanofiltration and reverse osmosis or membrane bioreactors in dairy wastewater treatment plants. Overall, the presentation will demonstrate that membrane processes are not only widely established in the dairy industry but have even the potential to enter new and to improve current applications.
Professor Frank Lipnizki, Department of Chemical Engineering Lund University, Sweden
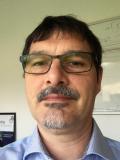
New membranes and membrane concepts for dairy applications
In 1998 Alfa Laval introduced membranes for the dairy industry with a polypropylene backing. This was done because the classical polyester backed membranes failed in cleaning procedures when applying harsh conditions such as high pH environments and temperatures. Polyester-based membranes require special cleaning formulations including lipases, proteases and surfactants whereas polypropylene backed membranes basically can be sanitised with sodium hydroxide solution at an elevated temperature to remove fatty acids. Over time the use of polypropylene backing based membranes has been copied by several other membrane manufacturers.Another focus in the dairy industry is energy saving. Low energy consumption can be achieved by proper process design. But what, if the plant has reached its capacity and no further infrastructural changes are possible? An effective membrane module design can help to achieve some extra room. Only small design changes can be made, but if the membrane itself or the spacer can be made thinner (same permeability) more membrane area can be fit into a module. Having more membrane area in a spiral module, however, automatically means that the production costs and consequently the module price will be higher. A lot of customers have become sensitive to environmental issues, thus asking for membranes using “green chemistry”. Many membrane manufacturers including Alfa Laval already use fully biodegradable solvents in production. European legislation, however, has decided to regulate the use of N-methyl pyrrolidone (NMP). Fortunately, NMP in membrane fabrication is used in very controlled conditions and the maximum exposure values are kept far below the maximum allowance. Also, the membranes are thoroughly washed and contain no hazardous substances. Nevertheless, the membrane industry needs to have new membrane concepts, for instance the use of sustainable solvents and polymers. To speed up this development, close collaboration between membrane users and membrane manufacturers is vital.
R&D Membrane Engineer Oliver Geschke, Alfa Laval, Denmark
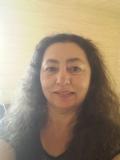
The interactions between fouling, cleaning and ageing of dairy membranes
The main bottleneck of skim milk ultrafiltration (UF) is flux mastering and fouling removal during cleaning. Over the last 10 years, the impact of the membrane chemical ageing due to the disinfection step was systematically studied. The selected membrane was a PES/PVP (HFK-131, 5-10 kg.mol-1, Koch). Its cleaning (1h, 50°C, 2 bar) was achieved by 2 formulated alkaline detergents: P3-Ultrasil 10®, Ecolab, 4 g.L-1 or Deptal UF L1® provided by Kersia, 5 g.L-1.Two main protocols were used:(1) filtering skim milk and cleaning & disinfecting solutions directly on spiral membranes(2) achieving filtration with flat membranes either pristine or voluntary chemically aged prepared using microwave (MW) activation simultaneously applied to soaking in the disinfecting solution [1,2], either sodium hypochlorite (NaOCl) (pH= 8.0, pH=11.5) or peroxide H2O2) + peracetic acid (CH3CO3H) (natural acid pH). A selection of results will be shown during the presentation: Misleading interpretations can be drawn from water flux measurement when dealing with the efficiency of chemical and enzymatic cleaning after nitric acid treatment for a pristine membrane [3,4]Changing UF at limiting flux (the maximum reachable flux commonly used at industrial scale) by UF at critical flux decreased the overall fouling, the irreversible fouling and moreover increased the cleanability of the pristine membrane [4]Disinfection steps used to ensure hygienic safety are generally achieved with NaOCl induced membrane accelerated ageing modifying both the critical and limiting fluxes but also the membrane cleanability [4]Misleading interpretations can be drawn from water flux measurement for NaOCl aged membranes as the opposite phenomenon can result: ageing induces a flux increase whereas the irreversible fouling increase induces a flux decrease [5]Comparison of chemical ageing due to NaOCl and H2O2 + CH3CO3H was systematically achieved confirming that oxygen is less aggressive than chlorine toward the membrane.
Professor Murielle Rabiller-Baudry, Institut des Sciences Chimiques de Rennes (ISCR) University Rennes, France